
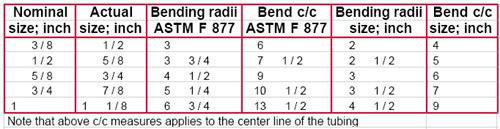
This new application calls for a 2-in.-OD tube with a 0.035-in.
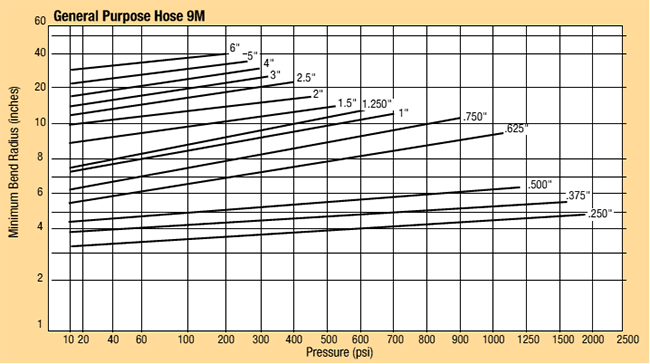
All seems right with the world.Ī few months go by and the same customer wants to trim material costs. So the fabricator sends a few bent tube samples to the customer, who then awards the contract that is sure to lead to lucrative recurring business. The first bend comes off the machine, and it’s perfect. After setting the machine program, the operator loads the tube and performs a test bend to see if the machine needs to be adjusted.

It looks like all the necessary tools to bend some prototypes are in the shop and ready to go. Tooling requirements are a bend die, clamp die, pressure die, mandrel, and a wiper die. The customer wants 200 pieces a week for a year. The application entails tube with a 2-in. The radius of a roll bent tube is no longer determined, however, by a matrix with fixed measurements, but by a set of three rollers that approach or distance themselves from one another, cold shaping the tube and impressing the desired radius.Īs for bending, we speak of the mean radius in case of round tubes, and of inner radius for tubular elements, but to calculate the feasibility formulas we will always have to refer to the mean radius.These wiper die inserts, designed to mount onto specific holders, help smooth out wrinkles in various tube bending applications.Ī customer reaches out to you with a tube forming job involving 90-degree bends. To remain in the same area as the previous example, for a tube Ø70 the minimum roll bend radius will be 350 mm and the maximum will be a theoretically infinite value. Unlike the bend radius, the roll bend radius is much greater and goes from 5 times the diameter of the tube to infinity. This is decisive for the purposes of feasibility of processing. They are the same as for the bend radius, but the coefficients that we will have to consider are different. Also when it comes to roll bending (or tube rolling) tubes, there are formulas for evaluation of the roll bend radius.
